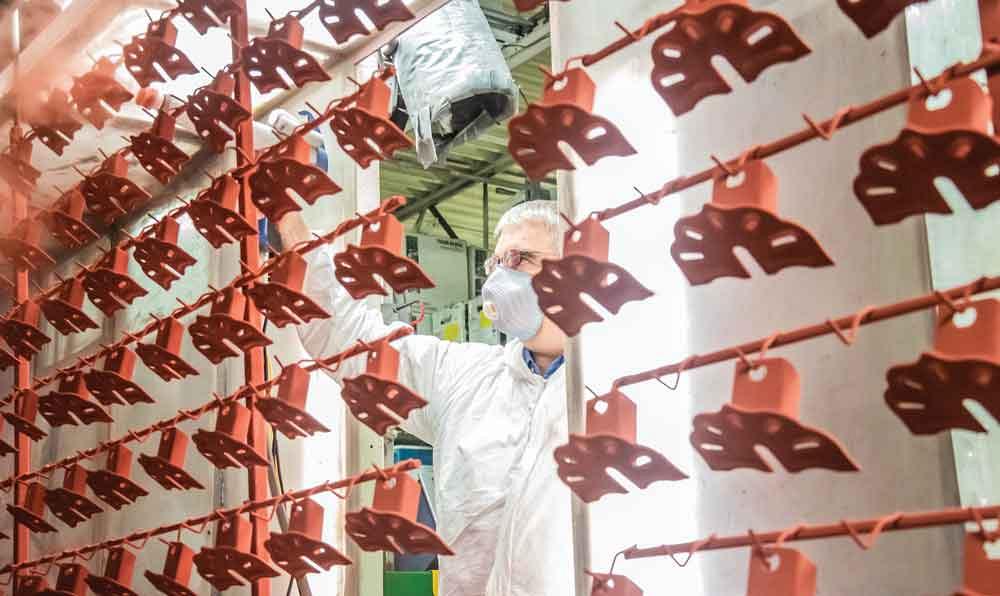
When PBZ experienced a slowdown in its agriculture market, the company expanded its powder coating services to compensate for it. Images provided by PBZ LLC
PBZ™ LLC, in the heart of northern Pennsylvania farming country that includes Amish communities, was founded in 1947 to supply agricultural parts and services to local farms. Even as the manufacturer grew alongside the other Paul B. Zimmerman companies, the ag market remained a staple of its business.
But as market forces created a downturn in the agricultural industry over the last three years, PBZ looked for growth opportunities elsewhere. It found that opportunity by expanding its powder coating capacity in its associate company, Keystone Koating.
“Since ag dropped off in the last three years, we’ve seen 10% growth year over year in our powder coating area. So even though the agriculture industry has softened, powder coating has grown rather significantly for us,” said PBZ President Richard Gehman.
Powder Coating Capacity
The manufacturer had switched from wet paint to powder coating applications years ago in a move to improve the durability of its paint operation for coating gates, stalls, and other barn equipment.
“Most if not all of our metal parts are powder-coated. Powder is as common as liquid, and it’s not uncommon for the under-the-hood or undercarriage parts to be powder-coated,” Gehman said.
So what do you do when you’re a fabricator with comprehensive metal manufacturing capabilities and you need something metal? You make it yourself. “One of the unique things about us is that we built our own powder coating equipment,” Gehman said. “So the spray booth, the cure oven, the dryoff oven, the pretreat system, the track system … we built all that ourselves.”
PBZ and its subsidiary, Keystone Koating, built three powder coating lines and an eight-stage pretreatment system for cleaning and preparing metal substrates for powder coating and finishing.
The company performs blast-cleaning to remove dirt, dust, and residue.
Expanding Above and Beyond
Keystone Koating provides powder coating as a service not only to the agriculture segment but to many industries, including construction, furniture, outdoors, and electrical industries, as well as for other manufacturers. “We powder coat quite a bit of office and outdoor patio furniture. We do get into some on-site furnishings such as benches, decorative railings, and trash cans. We’ll finish panels and light poles for the electrical industry segment. And we have another customer we do some carriage and buggy wheels and carriage parts for.”
Powder coating such a broad array of product types brought challenges.
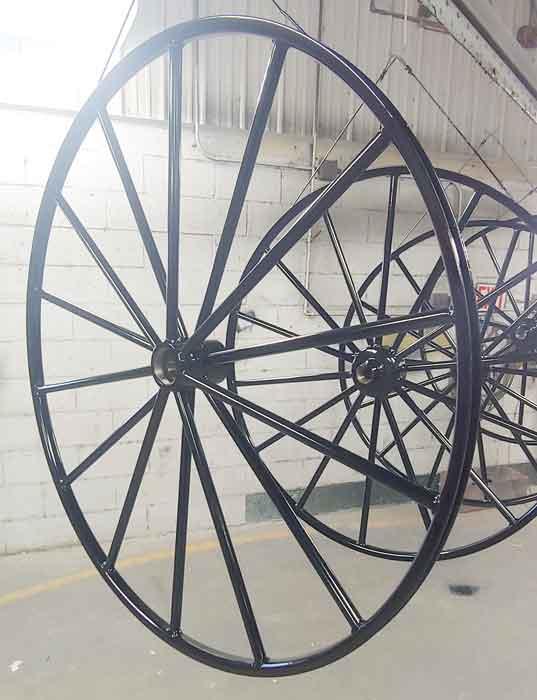
Oil and water seepage from the interiors of a carriage wheel during cookout required testing to determine where the leakage was occurring and why.
Overcoming Coating Challenges
“One of the things that we pride ourselves on is being a quality powder coater. To do that you have to be able to meet the needs of a variety of customers on a variety of substrates,” Gehman said. Some of the technical aspects of powder coating are obviously dealing with the substrate.
“We found that a good finish solution was to blast the part to a white metal blast before priming and powder coating it,” he continued.
Substrate. “So on our powder coating lines, we have an eight-stage pretreatment system. We have double rinses after our cleaner and conversion coating stages.”
Some people think eight stages is overkill, Gehman said. “But when you don’t rinse off your cleaner, especially a phosphate, you can dilute the effectiveness of each bath. This also causes you to use more chemicals. Our chemical supplier says we have one of the best-performing pretreat systems that they know of.
“What an eight-stage system also allows us to do is coat many different substrates well—anything from hot-rolled steel to cold-rolled steel, stainless, aluminum sheet and aluminum casting. A good pretreatment system leads to good adhesion and ultimately a good finish,” Gehman said.
“So, really, no matter what metal comes in, if we can blast the rust off and start with a clean substrate, we can perform powder coating on it really well.”
Product Characteristics. Every product has its own challenges to work through, based on the customer’s needs, expectations, and the characteristics of that given product, Gehman said.
“The science or the unique properties of the customer’s product and how it responds are other challenges,” he said. For example, a weldment may have some gas, oil, or water trapped inside the weld that gets “cooked out,” causing a defect on the product’s finish.
One such problem occurred when the company was powder coating a carriage wheel (see Figure 1). After it underwent all of the pretreatment and powder coating stages, some water and oil started leaking out of an inner compartment during the cure stage. Curing is when the part gets the hottest, with temperatures reaching to 400 degrees F. “That’s where the oil or water will come out,” Gehman said.
“The problem is, as it comes out on your finished product, you’re backed into a corner. Now what do you do? Well, you have to recoat it, but if you keep having to reject parts after they go through the oven, you’re going to have to find out a way to prevent the water or oil from getting inside.
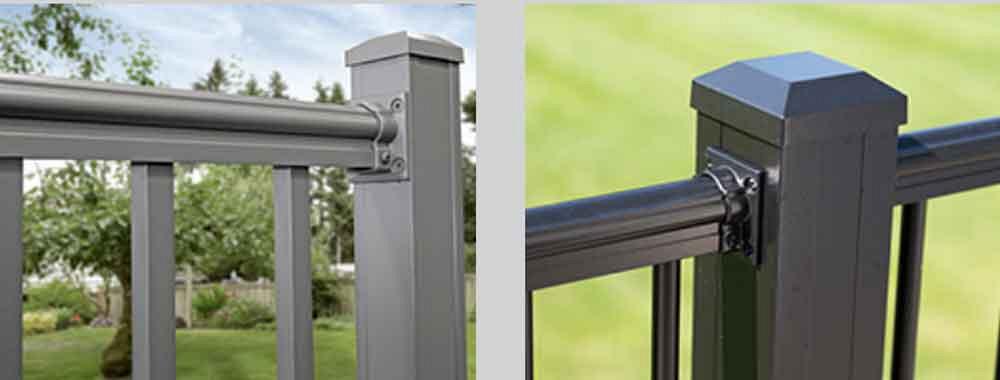
Finishing and powder coating an open-ended aluminum railing for a fence panel requires a different approach than a flat cold-rolled steel part, both because of the aluminum substrate and the part’s interior.
“Was there fluid inside the tube? Is it a weld issue? And if so, what do we have to do to eliminate the problem?”
Keystone Koating tested different methods to resolve the problem. Several experiments were run to figure out what the root cause was until it found the ultimate solution for the carriage wheel, but cookout is a recurring problem with some product configurations.
Isolating Problem Causes
“So we try a couple of different things—adjusting the temperature in pretreat and prebake. We might put an extra step in the process before we cure it just to make sure everything gets cooked out. And then sometimes we’ll consider taking away the pretreat stage altogether if we evaluate that there’s an unavoidable water trap. If we’ve tried all these methods and they don’t resolve it, we realize the problem may be in the weld. So we’ll go back to the manufacturer and say, ‘Hey, these are some of the problems we’re experiencing with your product. Can we partner with you to figure out a solution?’”
Gehman said that sometimes the problem lies in the stock material. A lot of oil residue may remain on the stock. “So we might ask them, ‘Can you go back to your supplier and see if they can get rid of the oil?’”
Keystone also might run tests on its pretreat system, adjusting the concentration or composition of the chemicals.
The company may put a lot of effort into resolving finishing quality problems, but Gehman believes it’s worth it. “You don’t want to cut corners even though it’s possible to do that in powder coating. We’re committed to not cutting corners. We have to have an efficient process while still providing a high-quality product.”
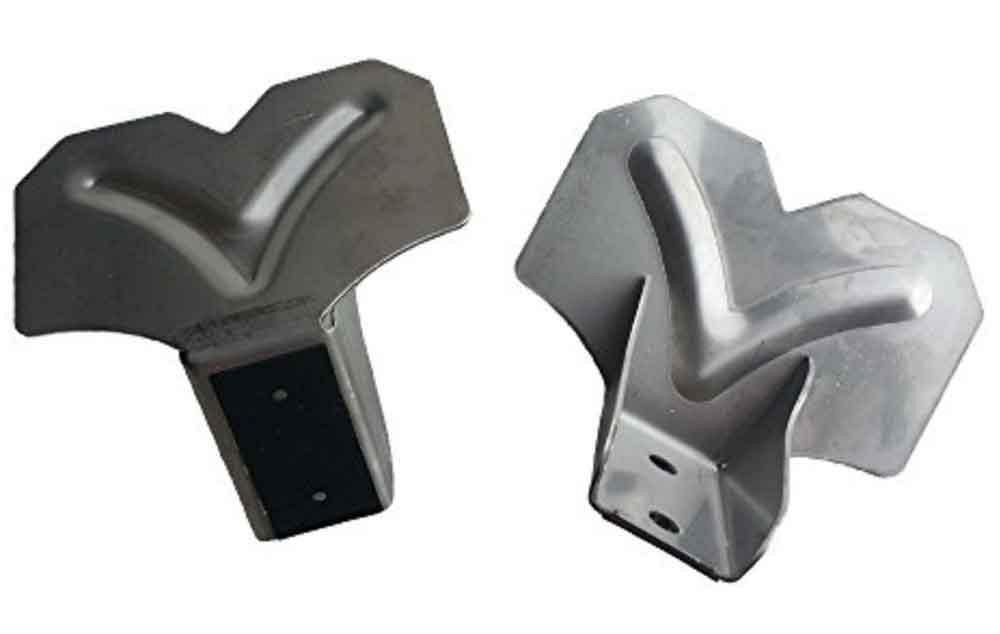
Keystone Koating powder-coats stainless steel snow guards, which direct snow melt on a metal roof for a client in the construction industry. Resolving problems with powder coating it to last long-term came down to increasing the action of the mechanical abrasion process.
"powder" - Google News
January 29, 2020 at 03:07AM
https://ift.tt/38K0zFY
Powder coating augments agricultural fabricator's bottom line - The Fabricator
"powder" - Google News
https://ift.tt/340CkR7
Shoes Man Tutorial
Pos News Update
Meme Update
Korean Entertainment News
Japan News Update
0 Comments:
Post a Comment